In the intricate world of food manufacturing, where precision and efficiency are paramount, the importance of proper lubrication cannot be overstated.
While lubrication may seem like a routine aspect of maintenance, its significance extends far beyond merely keeping the gears turning smoothly. The hidden impacts of approximate lubrication can reverberate throughout a food factory, affecting reliability, compliance, and ultimately, profitability.
Impact 1: Manufacturing Downtime Due to Equipment Failure
One of the most apparent consequences of approximate lubrication is an increase in manufacturing downtime. When machinery fails due to inadequate lubrication, production comes to a screeching halt. This downtime not only translates into immediate losses but can also have long-term effects on customer satisfaction and market reputation.
Impact 2: Unnecessarily High Maintenance Costs
Approximate lubrication practices often lead to accelerated wear and tear on machinery components. The result? Skyrocketing maintenance costs as frequent repairs and part replacements become the norm. Tight profit margins in the food industry mean that every pound spent on maintenance directly impacts the bottom line.
Impact 3: Production Losses and Reduced Overall Equipment Effectiveness (OEE)
Inadequate lubrication contributes to decreased Overall Equipment Effectiveness, a metric crucial for assessing manufacturing efficiency. Reduced OEE signifies lower production output, translating to lost revenue opportunities for food factories striving to meet market demands.
Impact 4: Inaccurate Lubrication
Approximate lubrication practices often involve time-based rather than condition-based PPMs. This lack of accuracy can lead to over-lubrication or, conversely, under-lubrication, both of which pose risks to equipment health. Over time, this inaccuracy can compromise the longevity and reliability of machinery.
Impact 5: Restricted Maintenance and Operator Lubrication Skillset
Improper lubrication can be traced back to a lack of training and knowledge among maintenance personnel and equipment operators. Investing in comprehensive training programs not only assures lubrication audit compliance, but also ensures that all staff members possess the skills required to execute precise lubrication practices, enhancing overall equipment performance.
Impact 6: Suboptimal Technician Productivity
When technicians spend an inordinate amount of time addressing issues arising from approximate lubrication, their overall productivity decreases as their frustrations increase. Time spent on reactive maintenance could be better utilised for proactive measures, thereby improving the overall health of the production line.
Impact 7: Audit Stress and Failures
Regulatory compliance is a critical aspect of the food industry. Approximate lubrication practices can lead to audit stress and, in some cases, non-compliance. Maintaining accurate records of lubrication practices is essential for demonstrating adherence to industry standards during regulatory audits.
Impact 8: High Levels of Reactive Maintenance
Approximate lubrication often results in a reactive approach to maintenance, addressing issues only when they arise. Shifting towards a proactive maintenance strategy reduces unplanned downtime and minimises the impact of equipment failures on production schedules.
Impact 9: Lower Resource Efficiency
Inefficient lubrication practices waste not only time but also valuable resources. Optimal lubrication minimises resource consumption, contributing to a more sustainable and environmentally friendly operation.
Impact 10: Higher Energy and Environmental Costs
The increased energy required to run machinery with improper lubrication contributes to higher operational costs and an elevated environmental footprint. Precise lubrication ensures energy efficiency, aligning with the industry's growing emphasis on sustainability.
Conclusion:
Proper lubrication is the unsung hero of a well-functioning food factory. The hidden impacts of approximate lubrication reach far and wide, affecting reliability, compliance, and ultimately, profitability. As the food industry continues to evolve, recognising the importance of precise lubrication practices is not just a matter of operational efficiency but a strategic imperative for sustained success.
Take advantage of our 4-week no-obligation lubricants trial:
Unlock the potential of Activate's BRCGS-compliant lubricants, storage systems, and equipment through a fully supported, no-obligation trial.
Fill in the form below to get started ↓
News and updates
The Hidden Impacts of Approximate Lubrication on Food Factory Reliability, Compliance, & Profitability
Contact us
Read On
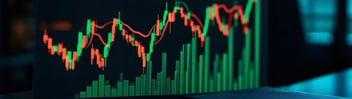
The Economics of Preventive Maintenance with Food-Grade Lubricants
Preventive maintenance is a cornerstone of efficient food manufacturing, ensuring operational...
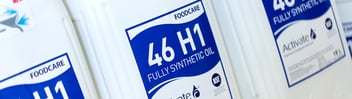
Best Practice Lubrication Benefits: A 5-step plan you can implement.
In the demanding landscape of modern food manufacturing, there's one component that often remains...
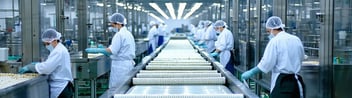
The Importance of Lubricant Compatibility in Multi-Line Food Production Facilities
Food production facilities operate multiple production lines, often with different types of...
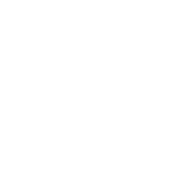
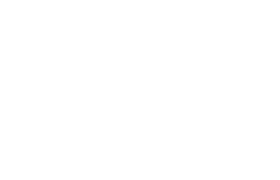
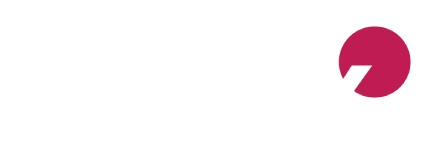

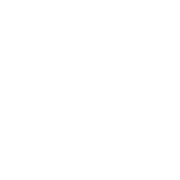
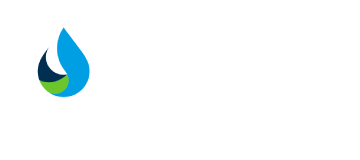